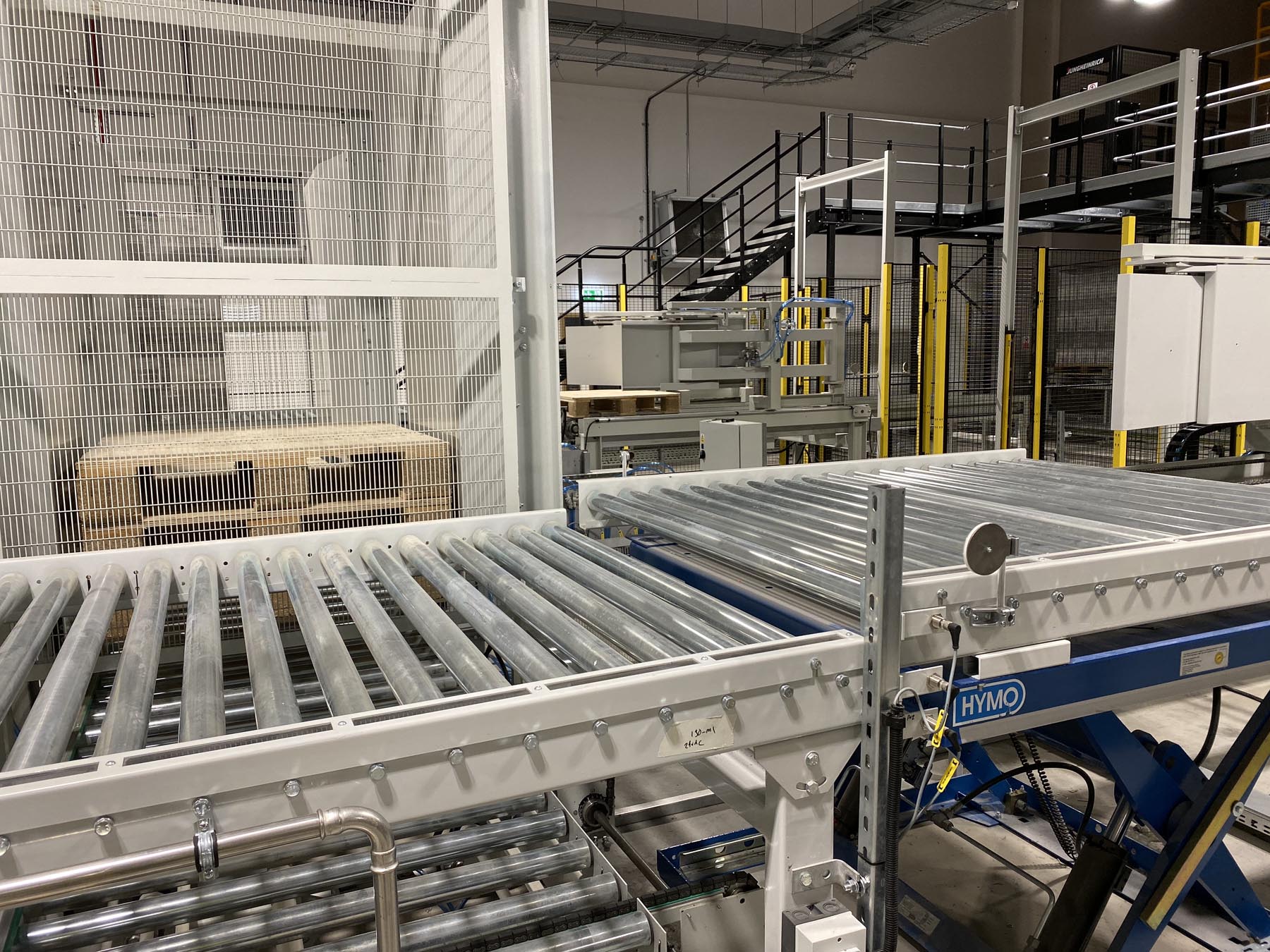
The challenge
Leading intralogistics provider Jungheinrich required support with the design, supply and installation of an advanced conveyor system (and associated equipment) for a new pallet exchanger system for their client Chivas Brothers. In addition to integrating seamlessly with the existing systems in place at the Chivas Brothers Dumbarton facility, the conveyor system would need to be able to process pallets of varying size at high speed, with 120 pallets per hour the set target to hit.
The project was part of a significant factory extension, incorporating a new high-bay warehouse designed by Jungheinrich to store boxed products on in-house pallets.
The Automatica solution
Working in close partnership with Jungheinrich, we quickly identified where our automation expertise would provide the greatest value for their whisky producing client.
The agreed solution began with pick and deposit stations and an inverted electrified monorail system, which transported the products on the in-house pallet system we designed specifically for the project. Next, the product was transferred from the in-house pallet to a slip sheet dispenser via sophisticated triple strand chain conveyors to ensure a smooth transition to transport slips.
The system's design also included two high-performance pallet exchangers and two pallet stackers, which enabled the efficient handling and storage of the in-house pallets. These pallets were then stacked and returned to the warehouse for reuse, optimising the cycle of resources.
Additionally, the integration of two slip sheet dispensers allowed for the precise placement of products onto transport slips, greatly enhancing the overall efficiency of the packaging process. The entire operation was supported by various 24v powered roller conveyors capable of handling pallets weighing up to 968kg, ensuring robust and reliable movement throughout the facility.
The result
The bespoke conveyor and pallet system provided by Automatica delivered Chivas Brothers with the enhanced operational capacity they desired and the pallet-per-hour results they demanded. The seamless integration of the solution with the existing equipment at the Dumbarton facility also ensured costly downtime and disruption was kept to an absolute minimum. A fact both Jungheinrich and Chivas Brothers were quick to toast.
Thirsty for industry-leading automation and innovation? Get in touch
Trusted by
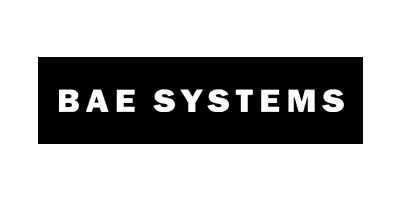
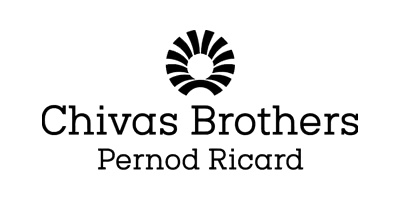
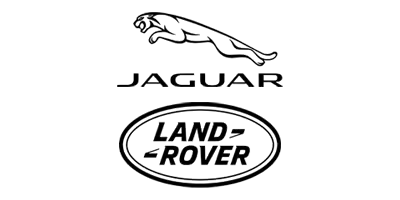
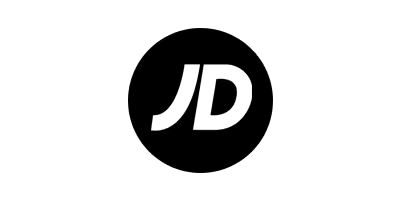
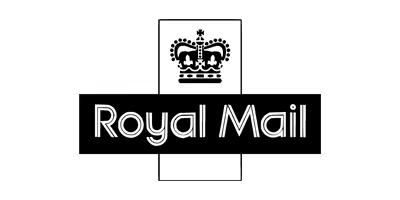
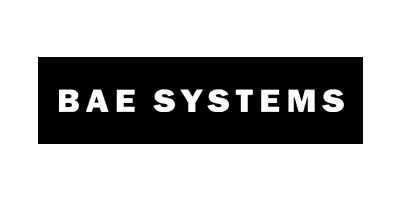
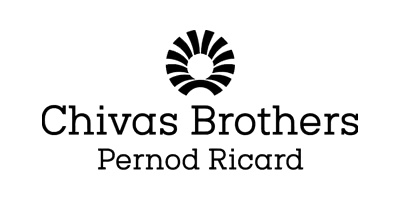
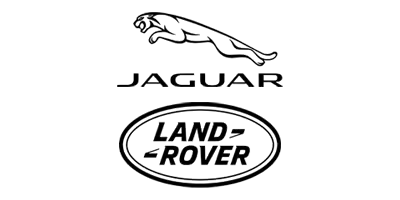
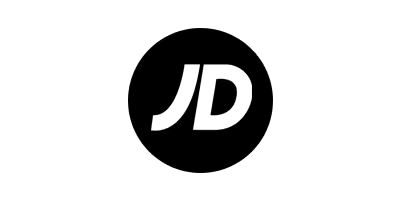
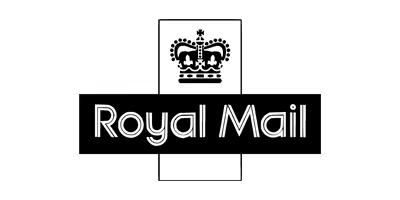