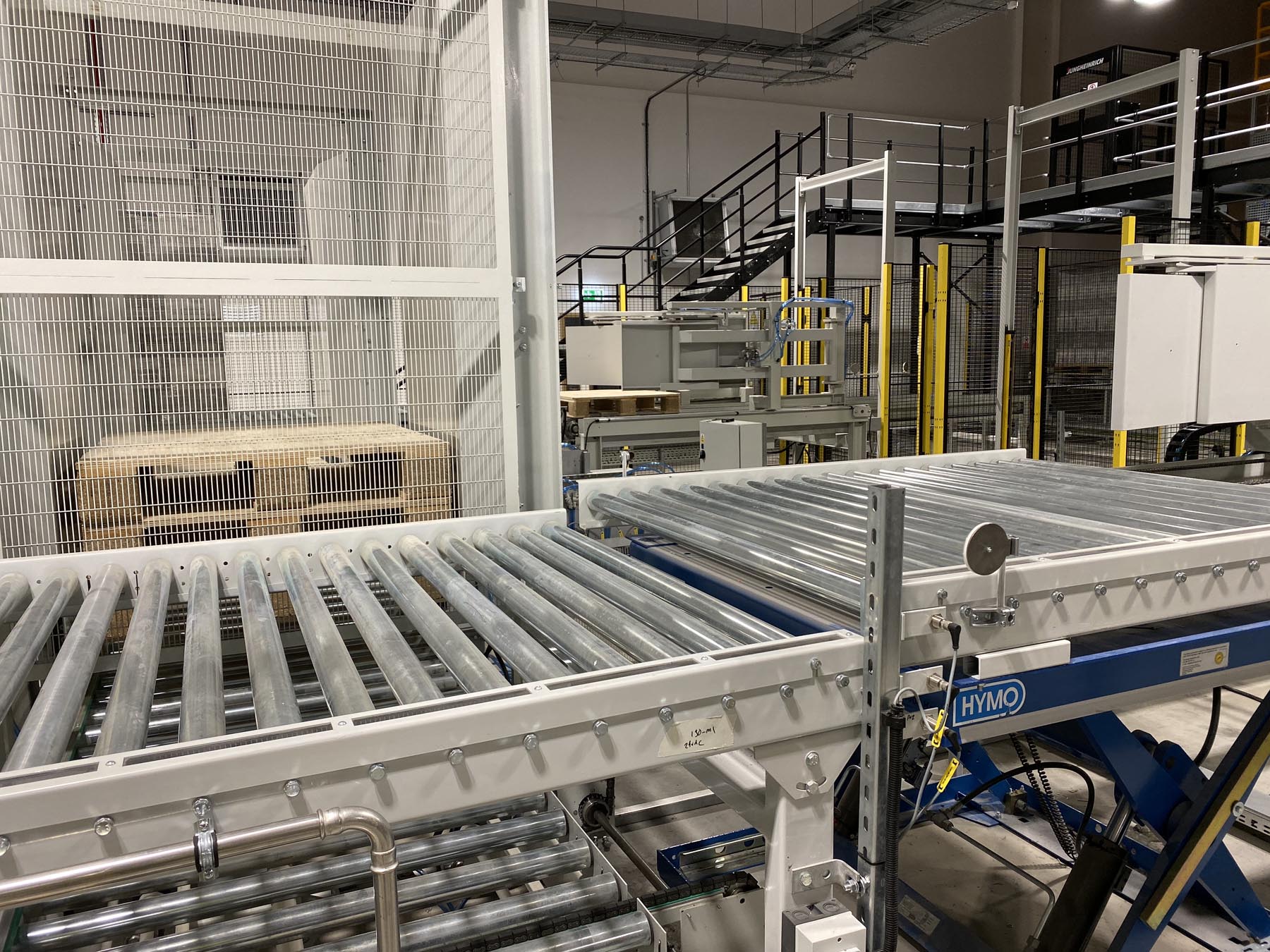
Automatica was commissioned by Jungheinrich to design, supply, and install an advanced conveyor system and associated equipment for a new Pallet Exchanger System at the Chivas Dumbarton Facility.
This project was part of a significant factory extension, incorporating a new High Bay warehouse designed by Jungheinrich to store boxed products on in-house pallets. The process begins with P&D stations and an inverted EMS system, which transport the product on the in-house pallet system implemented by Automatica. Here, the product is transferred from the in-house pallet to a slip sheet dispenser via sophisticated triple strand chain conveyors, ensuring a smooth transition to transport slips.
The system's design includes two high-performance pallet exchangers and two pallet stackers, which facilitate efficient handling and storage of the in-house pallets. These pallets are stacked and returned to the warehouse for reuse, optimising the cycle of resources. Additionally, the integration of two slip sheet dispensers allows for precise placement of products onto transport slips, enhancing the packaging process. The entire operation is supported by various 24v powered roller conveyors capable of handling pallets weighing up to 968kg, ensuring robust, reliable movement throughout the facility.
This bespoke conveyor and pallet system not only enhances the operational capacity at Chivas Dumbarton but also exemplifies the seamless integration of automated handling solutions in modern manufacturing environments. The project underscores Automatica' expertise in delivering tailored, efficient automated systems that align with the strategic needs of major industry players like Jungheinrich and Chivas Brothers.